Below is a guest post written by Terry Summers from Summertone Ltd. We first encountered Terry because of his expertise refurbishing analogue magnetic tape heads.
As one of the few, if not only, specialist UK-based company working in this area, we wanted to know more about Terry’s work. We were keen to understand the secrets of magnetic tape refurbishment, and whether Terry accepted that obsolescence for analogue media was imminent, as many audiovisual archivists claim. Many thanks Terry for taking the time to write the article, we hope you enjoy it.
***
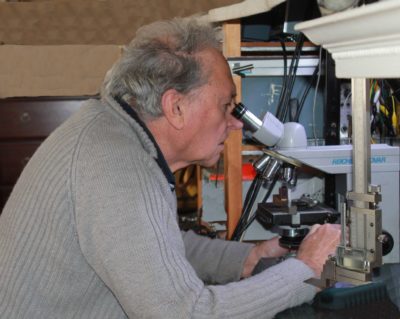
a gap inspection being carried out on an Ampex, half inch, two track, stereo replay head
Before I opened Summertone Ltd. I was for very many years, the Managing Director and magnetic head designer for the head manufacturing company Branch & Appleby. This was a specialist company serving the audio recording industry with magnetic heads as a supplier to Original Equipment Manufacturers in the analogue tape and film industry and for replacement heads for other types. B & A was particularly strong in the magnetic head supply for recording on perforated film for the synchronisation and editing of film sound, being the supplier of heads to many OEM studio film equipment manufacturers. The range of analogue heads designed and made by B & A was legion, ranging from 32 track 2 inch to 8mm film heads. B & A also supplied heads for other purposes, magnetic card readers and bank note verifiers being examples.
To be able to refurbish a magnetic head, it is essential to understand the working, the manufacturing principals and the materials used in it’s manufacture.
That expertise is with Summertone and is the reason for its success. The various magnetic materials used (mumetals of various grades, vitrovacs, ferrites etc.) each require specialist equipment and methods of surface finish to obtain intimate contact with the recording medium. A fact that is frequently overlooked is that a refurbished magnetic head has a performance that is superior to when it was new! The reason is that the magnetic losses due to the gap depth are less. So refurbishment not only restores the head’s ability to contact the magnetic material correctly, having removed the uneven wear caused by the abrasive recording medium, but also gives the head an improved performance, essential for the reproduction of archive, sometimes damaged material.
Digital Changes
The audio industry has of course changed with the coming of the digital age, some say for the better, but others disagree. We refurbish analogue heads for studios and individuals that are dedicated to the recording and reproduction of sound with the full complement of all the harmonics that are lost with a digital frequency cut off. We cannot hear them, but they colour the overall sound picture that we hear. That is the reason for the continuation of the use and restoration of the abundance of analogue machines by our studio customers (and some private users also).
The magnetic head is the vital link with the medium and is essential that it is kept in tip-top condition.
There are also many archival organisations that require the services of head specialists. The British Film Institute for instance, prides itself with the fact that the preserved sound it achieves is in many cases superior to the original public performances. This is due to their keeping their magnetic/optical sound pickups in excellent order and then, after transfer, using modern digital techniques to manipulate and store the results. Summertone receives heads from all over the world for refurbishment and is proud and pleased to say that the percentage of heads that it receives for refurbishment that are not able to receive suitable treatment, is very small indeed.
The scarcity of machines can be a problem, but as the number of studios using analogue machines diminishes they tend to pass to dedicated companies and individuals who appreciate their importance and who go to great lengths to ensure they are kept in a working condition or used for spares, not thrown in the skip. We appreciate that this cannot go on for ever, but the indications at the present time are that there are many who have the expertise to help in the specialist areas needed to keep archive machines in good working order.
It is a fact that the older analogue machines seem to be so well designed and built that they have very few faults that cannot be rectified easily. For instance, last week we switched on a 1960s valve recorder that had not been run for very many years. It performed perfectly. Another just needed a simple capacitor replacement for it to also perform. The point we are making is that the older technology was, and still is, reliable and understandable, unlike many modern machines.
It is possible to build new tape head blocks from scratch, but that is really not economical due to cost. We can, and do, still have replacement heads made to my designs but only if it is justified to keep a valuable, scarce, rare format, machines functioning. There are heads around, both new and second hand that can be refurbished. These can be obtained by combining two machines both for mechanical parts and heads. Summertone also has a small stock of heads.
Obsolescence
I do not agree with the archivists who say that there is a 10-15 year span left to transfer material. Magnetic tape and film has stood the test of longevity without deterioration which is why it is still being used for digital archiving. More modern archive methods have been failing. With good maintenance, analogue machines have a good life left and spares are still able to be obtained and manufactured as they are understandable to good engineers. I am sorry to say that when Summertone closes, our expertise for magnetic heads will be lost as it has not been possible to transfer a lifetime of analogue experience to another, due partly to the lack of financial incentive.